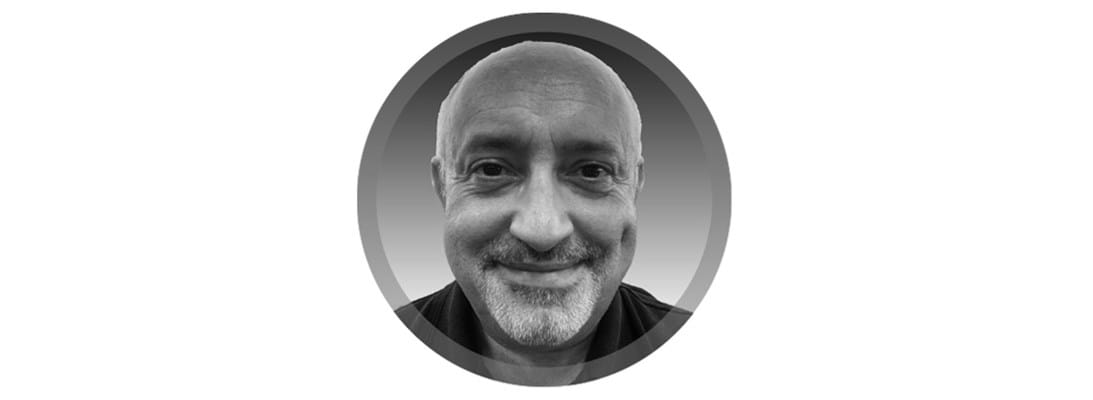
Paul Powers Sustainability at EnerSys
In August 2022, EnerSys set a climate goal to achieve Scope 1* greenhouse gas neutrality by 2040 and Scope 2* neutrality by 2050. While these goals are relatively new, the values of sustainability and efficiency have been embedded within the EnerSys culture since its inception, and have been top of mind for Paul Hebert, Engineering Manager at our Newport, UK plant.
Paul started at EnerSys in 1990 as a Junior Engineer. Nearly 33 years later, he’s still committed to making EnerSys plant processes and resource usage more cost effective and efficient as possible through a variety of projects. Before any of these projects are implemented, they must be vetted and approved by internal processes to show positive return on investment while also helping to achieve our climate goals. Although some are still in the works, we’re amazed by Paul’s ability to think creatively on how to make the plant even more efficient than it already is.
Here are some of the efficiency innovations Paul and his team have worked on:
- Lighting assessment. Paul and his team kicked off a survey at the start of 2023 to assess lighting usage and discover replacement opportunities throughout the whole plant. The survey will determine savings potential in both reducing kWh used in Newport and in cost reduction. To date, Paul and his team were able to replace lighting throughout the plants leading to an estimated annual savings of £13,440 GBP (about $17,200 USD) with more opportunities to be had.
- Smart inverter. Paul’s team is working to install new inverters and motors to control fan speeds throughout the manufacturing process (rather than relying on a one-size-fits-all fan speed). This will reduce the amount of kWh used in the plant because they are now able to customize the speeds needed for each process, rather than having high fan speeds for all purposes.
- Optimizing new equipment opportunities. Paul and his team have also made multiple upgrades to the gas-powered, drying ovens in Newport. One of the ovens used to dry plates has reached the end of its life after decades of use and is scheduled to be converted to electric, reducing natural gas usage. For other gas-powered ovens in Newport that are not yet ready for replacement, Paul ensures that the seals are maintained, and the doors are replaced as needed, in order to trap as much heat as possible within the system rather than letting heat escape. By improving the ovens to hold heat better, energy usage is decreased.
- Heat reuse. In some instances, ambient heat from certain manufacturing processes is unable to be retained, so Paul and his team are looking into options to recover that heat for other uses throughout the plant, such as water heating for showers.
- Solar. Paul’s team installed a small 6.5kw solar array in Newport. The solar array produces on average 23 kWh in 24 hours and is used to power lights, computers and fans throughout the plant.
Paul is also scoping out a variety of other projects to test viability and savings at the Newport, UK plant. The EnerSys team is also aware that what we learn from Newport’s projects can be implemented in other EnerSys plants across the globe using lessons learned thanks to our award-winning EOS program.
“I’m grateful for the opportunity to work for a company that gives me the opportunity to find projects that can improve what we do here every day at Newport,” said Paul. “Sustainability is important to me. I want to help make a better world for our kids, and I have the chance to do that at EnerSys in a way that benefits the company and the people I work with every day.”
*Scope 1 emissions are direct greenhouse (GHG) emissions that occur from sources that are controlled or owned by an organization (e.g., emissions associated with fuel combustion in boilers, furnaces, vehicles). Scope 2 emissions are indirect GHG emissions associated with the purchase of electricity, steam, heat, or cooling. Although scope 2 emissions physically occur at the facility where they are generated, they are accounted for in an organization’s GHG inventory because they are a result of the organization’s energy use.