Utilities and industrial plants depend on reliable and resilient backup power in case of an outage from the grid. Battery technology is a crucial link in the chain, acting as the primary energy storage and release source for uninterruptible power supplies and for other applications. Pure lead batteries, such as thin plate pure lead (tppl), have emerged as a proven technology for essential installations, but they must be sized and maintained correctly. This e-guide explains the advantages of tppl batteries for utility and industrial applications and provides a best-practice approach to implementing such solutions to maximize availability and lower through-life costs.
HOW MODERN THIN PLATE PURE LEAD BATTERY TECHNOLOGY PROVIDES THE KEY
INTRODUCTION
Batteries are vital to flexible power provision inside industrial and utility plants.
In electricity substations, for example, batteries provide critical backup as part of an uninterruptible power supply (UPS) in case of grid failure, ensuring continuous equipment operation. They could also be used for other activities such as load levelling and peak shaving and for integrating renewable energy from unpredictable sources such as wind farms.
Meanwhile, batteries are also used in a broad range of applications in manufacturing plants worldwide. They can potentially provide a highly effective means of energy storage for peak demand reduction during peak hours, lowering electricity costs.
In short, batteries are seen as a tried and trusted technology that can deliver flexible, reliable and sustainable power on demand in both utilities and industrial applications. Research shows that the market for batteries for applications such as utilities and industrial was valued at $21.2 billion in 2023 and is expected to reach $34.7 billion by 2029 – at an annual compound growth rate of 10.3%. Batteries are big business and will remain so as industrial and utility end-users increasingly look to electrify their operations.
This e-Guide, provides a timely explanation of the advantages of batteries for utility and industrial applications, focusing specifically on well-established pure lead chemistries such as Thin Plate Pure Lead (TPPL). It also provides a best practice approach to implementing such batteries in utility and industrial facilities to achieve maximum availability and lower through-life costs.
FLOODED BATTERIES HAVE THEIR DRAWBACKS
Historically, for battery users requiring a standby float—where a float charge is used to constantly maintain the batteries in a full state of charge so that they are ready to respond to any interruptions in the mains supply—the lifespan of batteries was deemed the most important criterion. Until now, most of these applications have primarily depended on using conventional flooded-lead acid batteries such as Vented Lead-Acid (VLA) batteries. Although these batteries have appeal in terms of longevity, some drawbacks are becoming more apparent.
Firstly, while the required energy density can be attained by correctly sizing VLA batteries, TPPL batteries have higher energy density and provide more power for the same footprint. This is an important consideration for increasingly space-constrained implementations in utility and industrial plants.
Secondly, ventilation is required for flooded battery types, which can have layout implications. Flooded batteries also require periodic maintenance, with the electrolyte needing to be regularly topped up. Finally, TPPL batteries accept quicker recharging than VLA, which is useful if further outages occur in close succession.
So, utility and industrial plant operators are now looking at other types of industrial batteries that combine longevity, energy density, and low maintenance. Consequently, Valve-Regulated Lead-Acid (VRLA) batteries, particularly TPPL, are finding appeal in this category.
UNDERSTANDING THE SHIFT TOWARDS TPPL
The development of VRLA batteries has overcome many of the limitations of VLA. By incorporating Absorbent Glass Mat (AGM) separators between their electrodes, VRLA has been able to mitigate electrolyte water losses (and the maintenance effort that comes with that). These batteries also attain considerably higher energy densities than VLA (flooded) cells and have much lower ventilation requirements, meaning that batteries may be installed next to the equipment they power. VRLA batteries no longer need to be kept upright but can be oriented as the application dictates. As the possibility of electrolyte spillage is eliminated, they are easier to transport.
The initial batteries used grids comprising materials such as lead-calcium (which are still used in some applications today). However, it is important to note that grid integrity in both lead-calcium and TPPL batteries deteriorates over time due to corrosion. The key difference lies in the corrosion mechanism and rate; lead-calcium grids tend to corrode faster than TPPL due to their grain size and inclusions.
The advent of TPPL technology has successfully advanced VRLA batteries significantly in other ways. The reduced thickness of the plates in TPPL batteries allows them to be packed closely together, providing a large reactive surface area and low internal resistance, which in turn enhances power densities. As a result, TPPL batteries can be recharged swiftly and are capable of delivering high current peaks without any voltage drop.
TPPL BATTERIES CAN BE RECHARGED SWIFTLY AND ARE CAPABLE OF DELIVERING HIGH CURRENT PEAKS WITHOUT ANY VOLTAGE DROP, TPPL BATTERIES ARE ALSO MAINTENANCE-FREE.
TPPL batteries are also maintenance-free. They are equipped with pressure relief valves that allow for the recombination of gases and open only when the internal pressure exceeds a predetermined threshold. Unlike some other battery types, TPPL batteries do not have removable caps or openings for water addition, as they do not require topping up with water – which eliminates maintenance and helps reduce the consumption of water. Another advantage is AGM technology, which absorbs the electrolyte into a glass mat separator between the plates. This design prevents the electrolyte from evaporating or spilling out, eliminating the need for topping up.
In addition, their gas emissions are extremely low. They have a long cycle life, especially when subjected to repeated microcycles of discharging followed by partial state of charge operation, in readiness for the next outage. Low self-discharge rates also allow battery storage for extended periods.
HOW TO RIGHT-SIZED TPPL SOLUTIONS
The inherent design of TPPL batteries allows utility and industrial users to select and install a solution that can offer multiple benefits, including extended service life, improved charge acceptance, high reliability and robust construction while maximising uptime and lowering maintenance. This selection can make life far easier for maintenance engineers and other hands-on team members within such plants. Adopting TPPL can increase resiliency, lower risk, deliver improved through-life costs, and better utilize maintenance teams' resources.
Let us look at how adopting TPPL batteries can deliver performance benefits in utility and industrial applications in greater detail. The first point in the journey comes with right-sizing the design. With many years of battery experience, EnerSys relies on highly competent and experienced technical teams to help guide end users to the most suitable product selection. This collaborative approach ensures optimized battery systems are correctly sized for their applications. These support teams take a technology-agnostic approach to battery specification – with a broad portfolio ensuring that the correct battery, not just any battery, is chosen.
Furthermore, online battery sizing tools provide an informed starting point. These tools - together with Carbon Footprint and Total Cost of Ownership (TCO) calculators - can determine the best configuration options for racks, accessories, and various room layouts. This is especially important in utility and industrial plants where space is constrained and environmental conditions might vary considerably.
EnerSys has a long track record in utility and industrial markets, so it has developed an overarching knowledge of battery technologies. Technical teams are encouraged to build long-lasting relationships and work in partnership with end users. This 'trusted advisor' relationship ensures that end users choose suitable battery architectures in the proper configuration for any deployment.
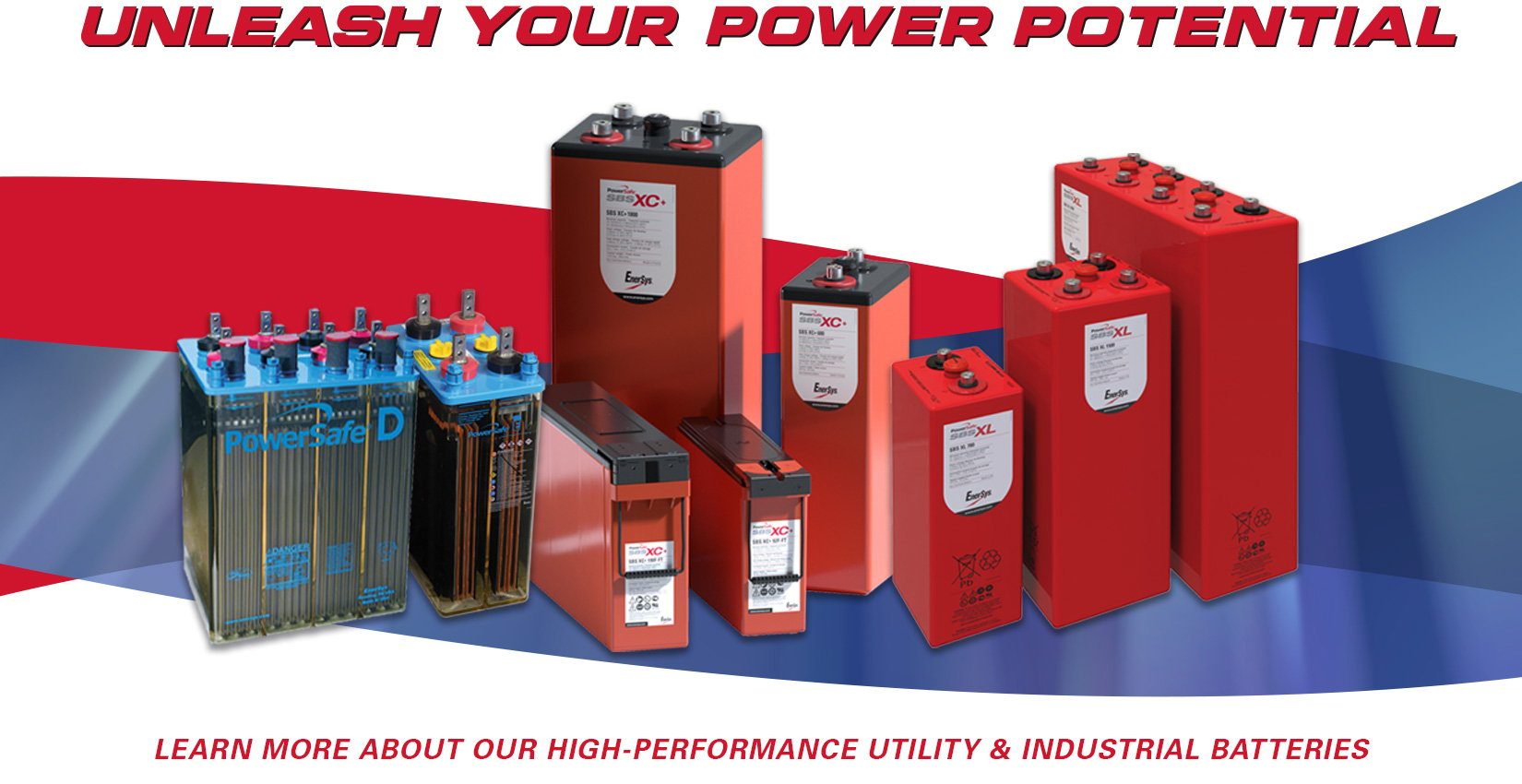
MAKING LIFE EASIER FOR MAINTENANCE TEAMS
Once selected and installed in the field, TPPL batteries can support more streamlined maintenance activities, improving the efficiency of overall site operations. Typically, maintenance managers and operatives are busy people. They perform an extraordinarily diverse hands-on role, carrying out routine inspections and preventive maintenance to various on-site strategies and timelines. Batteries are only part of a complex web of interconnected technologies. And when they underperform or fail, it requires time-consuming effort and resources to bring them back online.
Managing the logistics of maintenance schedules, especially for large-scale systems such as power stations or manufacturing plants, can be extremely challenging. So, the maintenance-free operation of TPPL batteries is a critical consideration. As previously mentioned, their inherent design characteristics mean they do not require regular watering or electrolyte checks, reducing the need for on-site maintenance visits. This characteristic significantly reduces the frequency of 'truck rolls' from exterior contractors to the site, minimizing logistical disruption to operations and reducing maintenance costs over the long term. Indeed, it is estimated that TPPL can deliver up to 50% maintenance cost savings compared to traditional flooded batteries over their lifetime plus the associated sustainability benefit created by reducing ‘truck rolls’.
THE ADVANTAGES OF FIELD-PROVEN SERVICE LIFE
TPPL also provides longer field-proven service life than traditional lead-calcium batteries. Fewer replacement parts can equate to an improved TCO. For example, change-outs for TPPL batteries are typically recorded at 8-9 years compared with 3-5 years for other technologies. These factors mean that TPPL batteries require replacement less frequently once installed, reducing the need for external site visits and associated downtime. These are essential considerations for maintenance teams, whose resources can be better used elsewhere.
THIS DESIGN INNOVATION MEANS THAT TPPL BATTERIES CAN ACHIEVE HIGHER CAPACITY LEVELS AND LONGER RUN TIMES WITH SMALLER UNITS, EVEN AS DISCHARGE RATES INCREASE, MAKING THEM MORE EFFICIENT AND DURABLE THAN TRADITIONAL LEAD-ACID BATTERIES.
TPPL offers a significant advancement in VRLA lead acid technology by reducing the grid corrosion, a common problem that leads to reduced battery life and performance.
In traditional lead-acid batteries, the positive grid, made of lead or lead alloys, supports the battery's Positive Active Material (PAM) and conducts electricity. However, this grid is prone to corrosion due to its operation in a sulfuric acid environment, leading to a loss in conductivity and an increase in grid volume as lead converts to less dense lead oxides. This corrosion reduces the battery's ability to conduct current and causes physical growth of the grid, which can disrupt the electrical contact between the PAM and the grid, ultimately resulting in battery failure. Factors such as float voltage, temperature, and particularly the purity of the lead influence the corrosion rate, with high-purity lead showing a slower corrosion rate than lead-alloyed with elements like calcium.
TPPL technology utilizes high-purity lead for the construction of the battery grids, significantly slowing down the corrosion process and maintaining the integrity and conductivity of the grid over time. This technology allows for thinner grids and, thus, thinner electrodes, increasing the number of electrodes that can fit within a cell and enhancing the reactive surface area and the efficiency of active material utilization. This design innovation means that TPPL batteries can achieve higher capacity levels and longer run times with smaller units, even as discharge rates increase, making them more efficient and durable than traditional lead-acid batteries that rely on thicker grids to compensate for rapid corrosion.
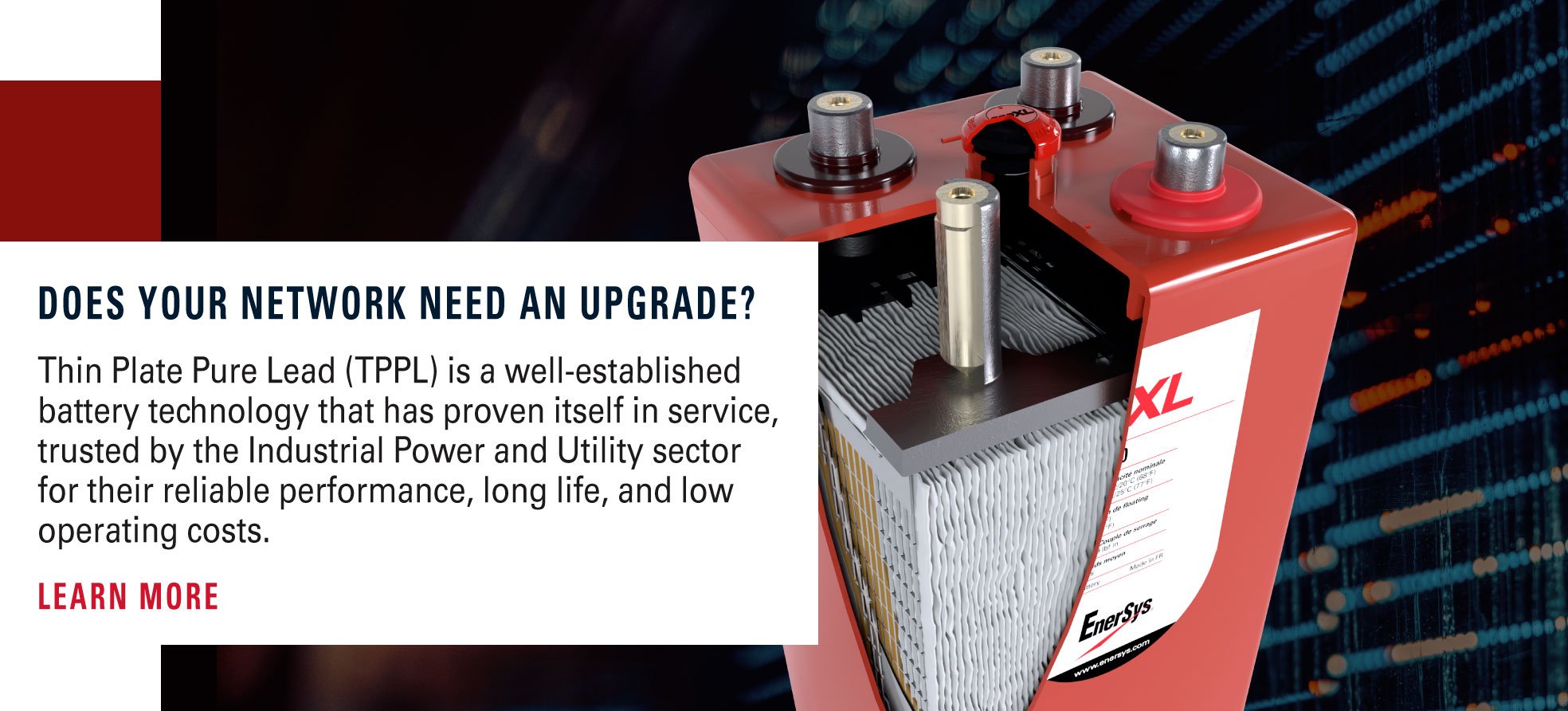
RAPID RECHARGE FOR RESILIENT OPERATIONS
TPPL also delivers other technical performance advantages, resulting in more efficient operations inside utility and industrial plants. For example, they typically have superior charge acceptance than traditional lead-acid batteries. They can recharge more efficiently and effectively, ensuring the batteries are ready to deliver power without prolonged charging times or excessive strain on charging systems.
With a larger reactive surface area available, TPPL offers the opportunity to reduce the recharge time of a UPS battery after a discharge event (provided that adequate recharge current is available). TPPL products, such as the PowerSafe® SBS battery series, do not require current limiting, provided the charge voltage is appropriately regulated. Batteries with TPPL technology will readily accept 1C (100A for a 100Ahr battery) until it approaches 80 to 85% State of Charge (SoC) while maintaining a very high level of energy efficiency. That means the battery can achieve 80% SoC in around 50 minutes following a full-depth discharge (and 100% SoC in less than 2.5 hours). Under the more typical condition of less than full discharge, the recharge times expected will be shorter.
Meanwhile, TPPL batteries are also very efficient on float charge due to lower internal resistance. Operating at a lower float current than conventional lead acid batteries reduces electricity consumption, therefore lowering Scope 2 emissions for the end user.
ROBUST MATERIALS AND CONSTRUCTION TECHNIQUES
TPPL batteries are also constructed with durable materials and advanced manufacturing techniques, making them highly resistant to mechanical damage and environmental stressors. This robust construction ensures that the batteries can withstand harsh operating conditions without compromising performance, reducing the likelihood of premature failure and the need for unscheduled maintenance activities.
Much of the robustness comes from a long track record of deployment into harsh operational environments, including military applications, which have resulted in a series of technical enhancements. The terminals were strengthened, and a more durable AGM paper was used between the plates. Many of the ideas were applied in the reserve power market and are used today to enhance the lifespan and performance of TPPL batteries, making them highly resistant to factors such as shock and vibration.
Also, in some parts of the world, such as the U.S., TPPL batteries are expected to provide reliable power during seismic events. Therefore, seismic testing to standards such as IEEE 693 is performed to meet seismic design recommendations for end-user applications such as substations. Seismic testing has informed certain design changes over the years to components such as the lugs used in batteries to provide a secure connection point for attaching cables or wires. In a world impacted by climate change and extreme weather events, EnerSys is committed to continued product evolution to ensure that batteries remain fit for purpose.
ENERSYS: YOUR PARTNER IN BATTERY POWER
In conclusion, pure lead batteries such as TPPL provide a reliable and sustainable option for utility and power plants. For maintenance managers and operatives looking to ensure uptime, often in challenging environments, benefits include:
- High Reliability
- Fast Recharge
- Wide Temperature Range
- Reduced Footprint
- Maintenance-Free
- Lower float current for energy savings
EnerSys has around 50 years of experience developing pure lead batteries such as TPPL. It offers a broad portfolio of robust, scalable and low-maintenance battery systems that provide the right-sized power for utility and industrial markets, regardless of the application. The products are made in first-class facilities in the US and Europe to the highest standards, backed by premium aftermarket care. Ultimately, these solutions provide reliable and sustainable power in factories and electricity stations, maximizing uptime and lowering through-life costs.