Pure lead batteries are increasingly recognized in the industrial and utility sectors for their high energy density and longevity. Beyond their technical prowess, these proven energy storage solutions also stand out for their sustainable lifecycle benefits. This e-Guide examines how pure lead batteries support sustainability through efficient performance, minimal maintenance, and full recyclability. It also underlines how adopting pure lead batteries helps industrial and utility organizations streamline operations, optimize costs, and enhance reputation en route to net zero.
INTRODUCTION
Industrial and utility organizations are increasingly seeking to deploy more sustainable technologies and processes across their operations. Several motivating factors are driving this transition. More environmentally friendly systems and solutions can deliver cost savings and reduced through-life costs – for example, by reducing energy bills and overall resource consumption – while helping to ensure regulatory compliance and mitigate risk. They can also play a significant role in enhancing reputation and branding at a time when stakeholders increasingly expect businesses to operate more responsibly.
Statistics tell the story of this shift to adopt cleaner processes and technologies. A recent Deloitte survey revealed that 85% of business leaders said they increased investments in sustainability in 2024 — up from 75% in 2023 — and half started implementing technology solutions to help achieve climate goals. Meanwhile, data from the National Association of Manufacturers in the US found that nine out of ten members agreed that sustainability is a top priority and that the sector has a special responsibility to society to transition to a future economy based on more circular methodologies. Major European companies are also committed to a shift to more sustainable operations, says the European Environment Agency, with average scores for environmental, social, and governance rising to 80.6 in 2024, reflecting a strong commitment to aligning with climate targets.
The scene is set, then. Industrial and utility organizations want and expect to adopt more sustainable processes and technologies, and this can be done in numerous ways. Many organizations are increasingly looking to improve the efficiency of internal operations and are investigating the use of renewable energy sources within facilities to decrease direct and indirect greenhouse gas emissions. Within the same context, other initiatives aim to reduce waste and increase responsible water management to protect valuable natural resources. These companies want to deploy well-designed products and systems that make effective use of raw materials, have low maintenance requirements, and can be recycled at the end of life. In short, by embracing sustainable technologies, industrial and utility companies can achieve long-term resilience and competitiveness while contributing positively to environmental stewardship.
SUSTAINABILITY IN ACTION
So, what does this sustainability agenda look like inside EnerSys – one of the world’s leading suppliers of industrial batteries? How is the company driving change at a top-line level? More specifically, how is EnerSys positively impacting the way that Thin-Plate Pure Lead (TPPL), is designed, built, operated, and disposed of within the industrial and utility sector?
Company-wide, ESG goals have been set that reinforce EnerSys as a sectoral leader. For instance, the company aims to reduce energy intensity by 25% per kWh of storage produced by 2030 vs 2020. As of the end of 2023, there has been a 13.3% reduction since the start of the decade. EnerSys also has an ambition to become CO2 neutral for Scope 1 emissions by 2040, and considerable progress has already been made. Emissions are 25% lower in absolute terms compared to 2019.
COMPANY-WIDE, ESG GOALS HAVE BEEN SET THAT REINFORCE ENERSYS AS A SECTORAL LEADER.
Such notable achievements are the sum of many parts. EnerSys has battery design and manufacturing facilities located all over the world, including Europe and the U.S. In each case, there is an ongoing effort to reduce the environmental impact of the manufacturing processes while delivering sustainability advantages across product lifecycles through lower maintenance and ease of recycling. These initiatives are all aimed at helping industrial and utility organizations meet their environmental objectives en route to net zero.
ENVIRONMENTALLY-CONSCIOUS MANUFACTURING
Let us look at what that means in terms of practical, real-world examples. Pure lead batteries represent a tried and trusted technology for uninterrupted power systems inside industrial and utility companies due to their inherent high energy density and reliability. But how can they be made in a more environmentally conscious manner? And how can sustainability advantages be derived at the point of use? The manufacturing process is an excellent place to start, with plant location playing an important part in the story. For Europe and the U.S., EnerSys® TPPL batteries are designed and built close to their point of use, keeping transport to a minimum.
Furthermore, many countries home to EnerSys production facilities, such as France, the UK, and the U.S., have invested significant amounts into lower-carbon electricity networks compared to other parts of the world. France, for example – home to the Arras production facility, which employs more than 750 people – benefits from decarbonized electricity and has the lowest per capita emissions of major economies due to the role of nuclear energy. According to the World Nuclear Association, 70% of power in France comes from nearly zero carbon nuclear, while hydropower, a carbon-free renewable energy source, supplies an additional 10%. Also, the UK and the U.S. have relatively high percentages of clean energy compared to many other countries, which positively impacts the carbon footprint of batteries made in these regions.
Individual EnerSys plants have also invested in renewable energy projects. For example, the Bellingham, Washington facility in the U.S. uses clean energy generated by a 32.4kW solar array. Since its installation in 2015, it has generated over 200,000 kWh, and EnerSys is currently installing a 5.2 MW array at its global headquarters in Reading, Pennsylvania, U.S.
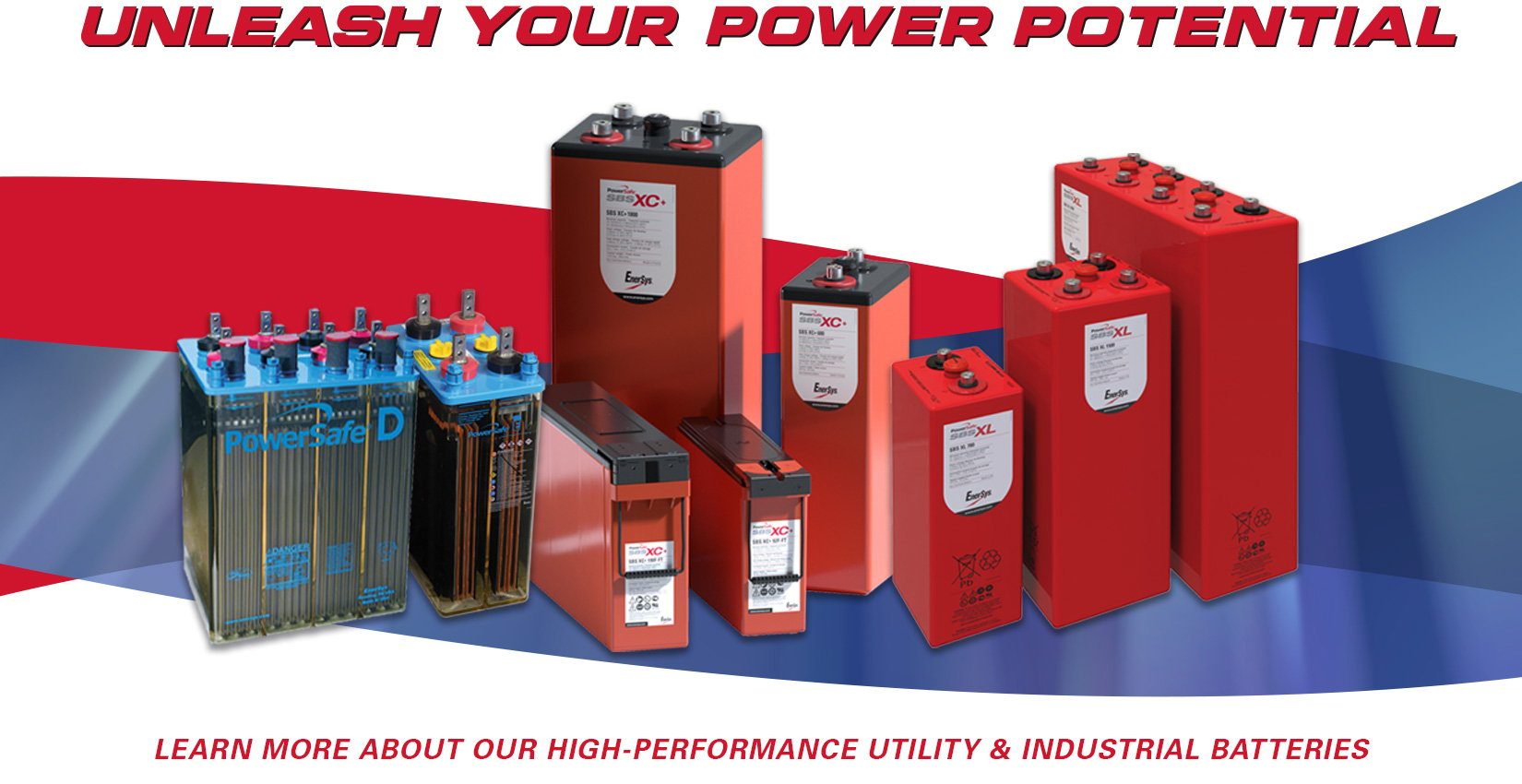
INVESTMENTS IN PRODUCTION TECHNOLOGIES
Energy efficiency is good for the planet and the bottom line. Inside plants, investments have been made to reduce the environmental impact of the battery production process. Historically, pure lead batteries, including TPPL, have involved a lot of manual hands-on processes such as lead paste preparation, battery grid fabrication, plate pasting and curing, and assembly of cells. In post-production, employees would also be involved with quality control and inspection, finishing, labelling, and packaging. These days, many of the manual processes have been automated to achieve better optimization of materials, higher production speeds, improved product consistency, reduced waste and enhanced quality. As a case in point, at the EnerSys Springfield, MO plant in the U.S., millions of dollars have been invested on a highly automated and digitized high-speed line to increase output and reduce energy consumption. Internal studies have shown that reducing the amount of human interaction in the manufacturing process – with less manual handling activity on the production line – can increase efficiency, quality, and accuracy, thus reducing the need for rework. This transition to more automated operations frees staff to perform more value-added roles, resulting in more streamlined operations and lower associated waste and energy costs. More generally, EnerSys continues to look at how advanced technologies such as automated guided vehicles, robotics, conveyors, and vision systems – often underpinned by rapidly evolving disciplines such as artificial intelligence and machine learning – can be adopted in production environments to reduce the environmental impact of its battery manufacturing activities.
Other production initiatives can also reap rewards. The manufacturing process for lead batteries requires melting lead in pots for casting and grid production. Traditionally, this process involves heating several tons of the metal with a large, gas-fired burner. Not only does this process produce greenhouse gas emissions from combustion, but it also has less than optimal effects on the equipment. Gas heating is inefficient, as the direct application of heat to melt lead can cause stress in steel pots and ultimately result in cracks over time. A cracked pot can lead to a potentially dangerous situation for both our workers and the environment.
With safety and environmental stewardship in mind, EnerSys has decided to transform into a safer process. The energy required for heating will now come from electricity, which is increasingly produced from renewable sources. Electrification of the melting process lowers the carbon footprint of the batteries being made. Alongside electrification efforts, EnerSys is continuously seeking to refine and improve other aspects of the melting process to further reduce the carbon footprint of its batteries. Furthermore, as our electrical transmission and distribution grids decarbonize—and batteries play a role in that too—the process approaches carbon neutral, which would not be possible with gas-fired processes.
EnerSys has also adopted a new lead battery manufacturing technique at selected plants in the U.S., France, and Poland, which further eliminates the need for traditional energy-intensive lead heating, melting, and cooling processes. The Sovema Cold Cube cutting system uses a cold process to trim lead directly from its solid state into cubes of the necessary thickness. By replacing conventional gas fire processes, EnerSys has achieved a reduction of approximately 0.5 kilograms of CO2e per battery produced, equating to a ~20% decrease in embedded Scope 1 Greenhouse game emissions per battery. The new process significantly reduces employees' exposure to lead in the work environment, mitigating potential health risks associated with traditional manufacturing methods.
Meanwhile, EnerSys saves approximately 495,000 gallons of water per year at each site that uses the Cold Cube cutting system by eliminating the need for water cooling in the cube production process, contributing to water conservation efforts. By eliminating the need for exhaust ventilation to remove lead fumes and the lead recovery process, environmental lead emissions to the atmosphere have been reduced while lead waste has decreased by tens of thousands of kilograms per year. The Cold Cube cutting system is being implemented at additional EnerSys manufacturing facilities, extending its positive impact beyond its initial deployment.
Furthermore, for products such as pure lead batteries, EnerSys instils stringent quality and traceability methodologies to ensure optimized materials usage. Each plate used in the production process is weighed and date-stamped to ensure process repeatability and consistency while minimizing waste. EnerSys is also committed to environmental standards such as ISO 140001 to drive continuous improvement across its operations.
CASE STUDY: ENERSYS® BATTERIES PROVIDE SUSTAINABLE BACKUP FOR KOSOVAN POWER PLANT
EnerSys® Thin-Plate Pure Lead batteries have improved the reliability and sustainability of Kosovo Energy Corporation (KEK) power infrastructure, providing uninterrupted operations in the event of grid failure.
Existing batteries at the KEK Termocentrali Kosova B (TCB) plant had reached the end of their life and were deemed a risk to backup power reliability. The plant operator sought a solution with lower maintenance requirements than the existing flooded battery installation. The solution was to integrate PowerSafe® SBS XL 2 Volt batteries, overseen by EnerSys regional distributor EXBATT. The batteries offer superior performance and extended life compared to the existing conventional solutions. Importantly, they can operate maintenance-free, reducing the maintenance workload and costs associated with upkeep—delivering a sustainability advantage. The batteries were installed in a new vibration-resistant racking system for long-life operation.
THE SOLUTION WAS TO INTEGRATE POWERSAFE® SBS XL 2 VOLT BATTERIES, OVERSEEN BY ENERSYS REGIONAL DISTRIBUTOR EXBATT. THE BATTERIES OFFER SUPERIOR PERFORMANCE AND EXTENDED LIFE COMPARED TO THE EXISTING CONVENTIONAL SOLUTIONS.
Key technical characteristics included high-temperature operation. PowerSafe® SBS XL batteries have robust temperature tolerance, enabling them to operate efficiently even in elevated temperatures. This feature ensured that KEK's battery room, with temperatures ranging from 25-40°C (77-95°F), could still benefit from reliable battery performance until an air conditioning system is activated.
"I am thrilled to highlight our team's exceptional collaboration in transforming KEK's power infrastructure with the flagship PowerSafe® SBS XL battery range from EnerSys®," said Blerim Blaku, Director at EXBATT. "Together, we have achieved remarkable reliability and helped to ensure uninterrupted operations during technical breakdowns at Kosovo's leading electricity generator. The dedication and expertise of our team, combined with outstanding solutions and support from EnerSys®, have paved the way for a resilient future for Kosovo's grid."
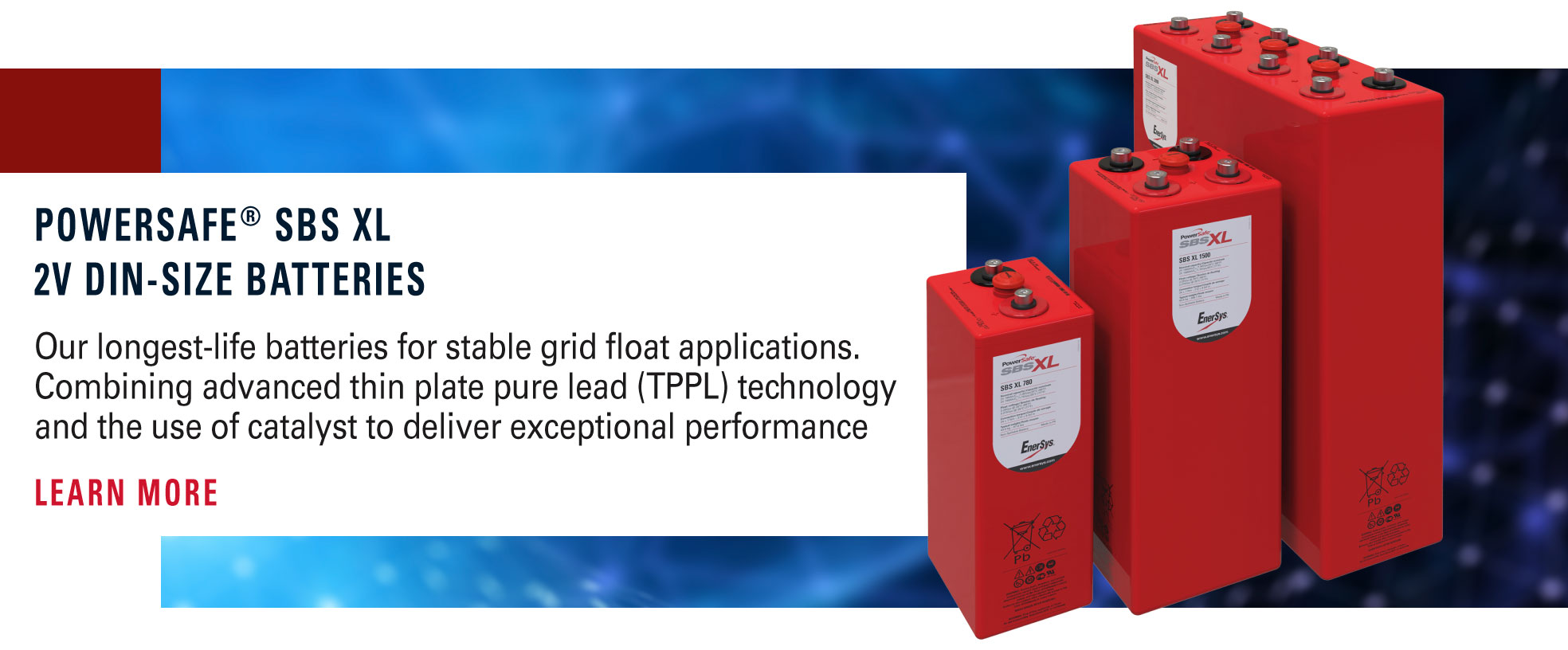 |
REDUCING ONSITE MAINTENANCE
So, that outlines some of the sustainability benefits gained from developing internal processes. However, the environmental advantages of pure lead batteries within industrial and utility applications extend to operation, maintenance, and end-of-life. In terms of applications, pure lead batteries are used for multiple use cases in such environments, providing reliable backup, supporting renewable energy integration, powering critical equipment, and enhancing overall resiliency. They are routinely selected due to their inherent technical capabilities, such as long life cycles, high energy density, fast charging, and reliable performance in extreme conditions. Pure lead batteries also encourage the uptake of more electrified onsite systems and technologies rather than, say, diesel or gas-powered solutions for vehicles, equipment, or backup power, which would have far higher emissions at the point of use.
However, the most significant sustainability benefit is derived from more streamlined maintenance activities, which are derived from inherent design and manufacturing characteristics. Pure lead batteries use high-quality materials, thin plates, and advanced sealing techniques, giving them a lifespan of up to 15-20 years. Reduced gassing and high recombination efficiency within batteries minimizes water loss, reducing the need to top up the electrolyte with distilled water. Also, pure lead batteries are more corrosion-resistant than other battery chemistries. Furthermore, the overall enclosure (container and lid) in which each battery is housed exhibits industry-leading robustness. The ability of these enclosures to deal with heavy shocks and vibrations supports longevity in the field.
These factors, in combination, reduce the need for regular maintenance activities and associated 'truck roll' visits to the site. Lower maintenance requirements of batteries with TPPL technology, compared to traditional battery types, translate to fewer resources consumed and less environmental impact over the lifespan. Meanwhile, pure lead batteries are also very efficient on float charge due to lower internal resistance. Operating at a lower float current than conventional lead acid batteries reduces electricity consumption, therefore lowering Scope 2 Greenhouse emissions (from electricity) for the end user. Ultimately, pure lead batteries offer reliable and low-maintenance performance in industrial and utility environments - reducing lifecycle costs and enhancing sustainability credentials.
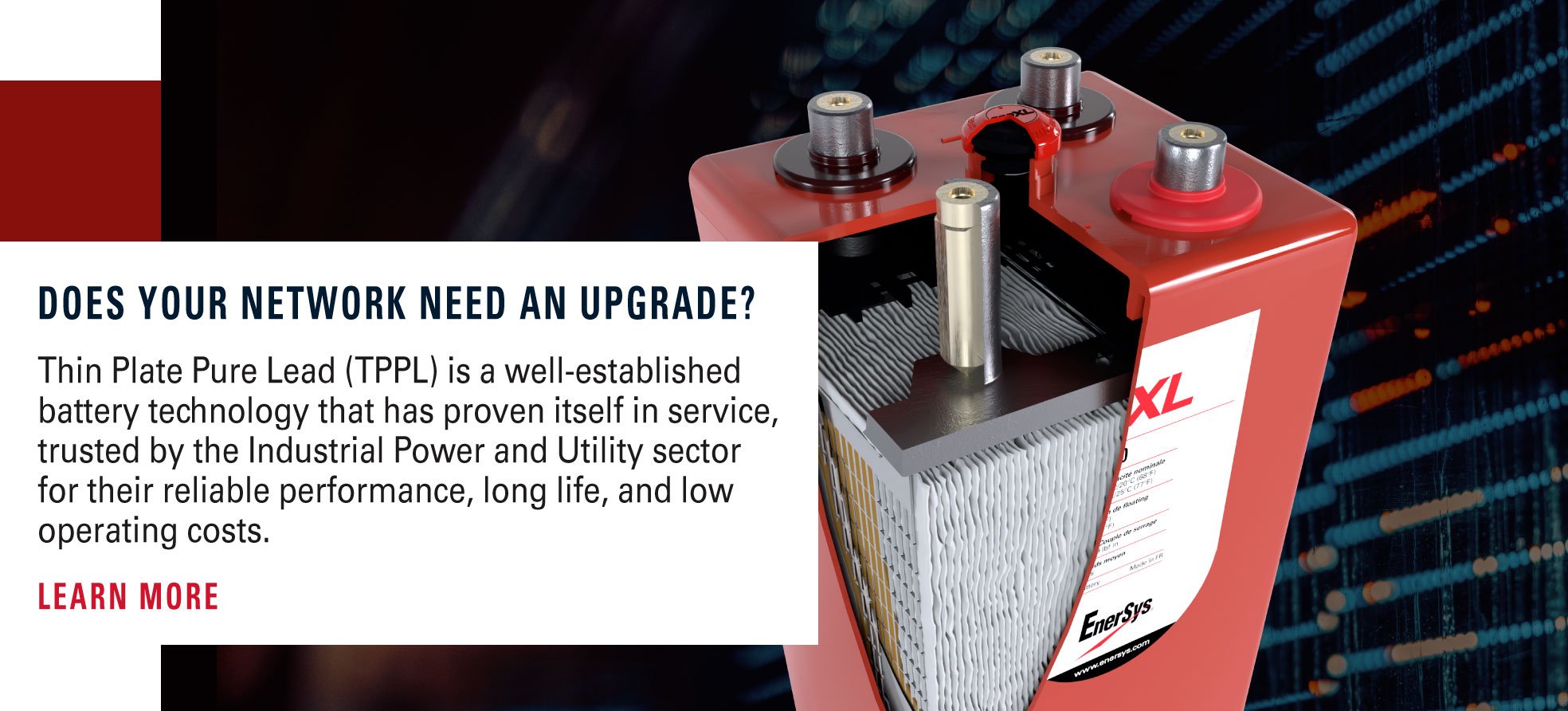
RECYCLING ALL MAJOR COMPONENTS
Eventually, though, all battery products reach their end of life. There is also a sustainability story to be told with recycling and reuse coming into play as part of the circular economy. Research from the Battery Council International (BCI) shows that lead batteries' three main components (lead, plastic, acid) are 100% recyclable. Lead ingots are used to manufacture new battery grids, while plastic is recovered to make new covers and cases. Meanwhile, electrolytes can also be reclaimed and reused in manufacturing new batteries. In other cases, compounds such as sodium sulfate can be separated from used electrolytes and recycled or sold for use in textile, glass, and detergent manufacturing. According to BCI, these processes create the raw materials needed for new conventional lead batteries, and a new conventional lead battery is formed of at least 80% recycled material; indeed, conventional lead battery manufacturers in the U.S. source 83% of the needed lead from North American recycling facilities.
RESEARCH FROM THE BATTERY COUNCIL INTERNATIONAL (BCI) SHOWS THAT LEAD BATTERIES' THREE MAIN COMPONENTS (LEAD, PLASTIC, ACID) ARE 100% RECYCLABLE.
This well-established, closed-loop life cycle means lead batteries, which according to BCI are the most recycled consumer product in the U.S., are a hugely advantageous component of the transition to a low-carbon, circular economy. Looking forward with the maturity of other battery chemistries in mind, EnerSys is also working in collaboration with trade associations and other stakeholders to instigate a similar recycling process for lithium-ion batteries, which contain metals like lithium, cobalt, nickel, and copper. This chemistry brings different challenges at the end of the lifecycle, and EnerSys is helping develop new processes and technologies for recovering lithium-ion battery parts that are less impactful on the environment, whether that is through a lower carbon footprint or producing less synthetic chemicals that can cause ecological damage. This ongoing work will continue to feed into the sustainability narrative around new energy-storage products.
SUPPORTING END USERS EN ROUTE TO NET ZERO
It is clear that pure lead batteries present a compelling technology solution for industrial and utility organizations looking to enhance their environmental credentials en route to net zero. Pure lead batteries represent a tried and trusted technology for multiple applications in these environments due to their inherent high energy density, reliability, and other technical performance characteristics. But they deliver many sustainability advantages, too – from the point of design and manufacture through to operation, maintenance, and end of life. EnerSys has manufactured industrial batteries for over one hundred years, putting it at the forefront of manufacturing capabilities and new product development. The company is committed to continuously improving its products and processes, with ongoing investment into sustainability initiatives throughout the lifecycle. Other tools, such as online carbon calculators, support these advances, helping customers make more informed product choices. Ultimately, it is about ensuring that pure lead batteries continue to provide stable and reliable energy storage while contributing to the cleaner and more distributed energy networks of tomorrow